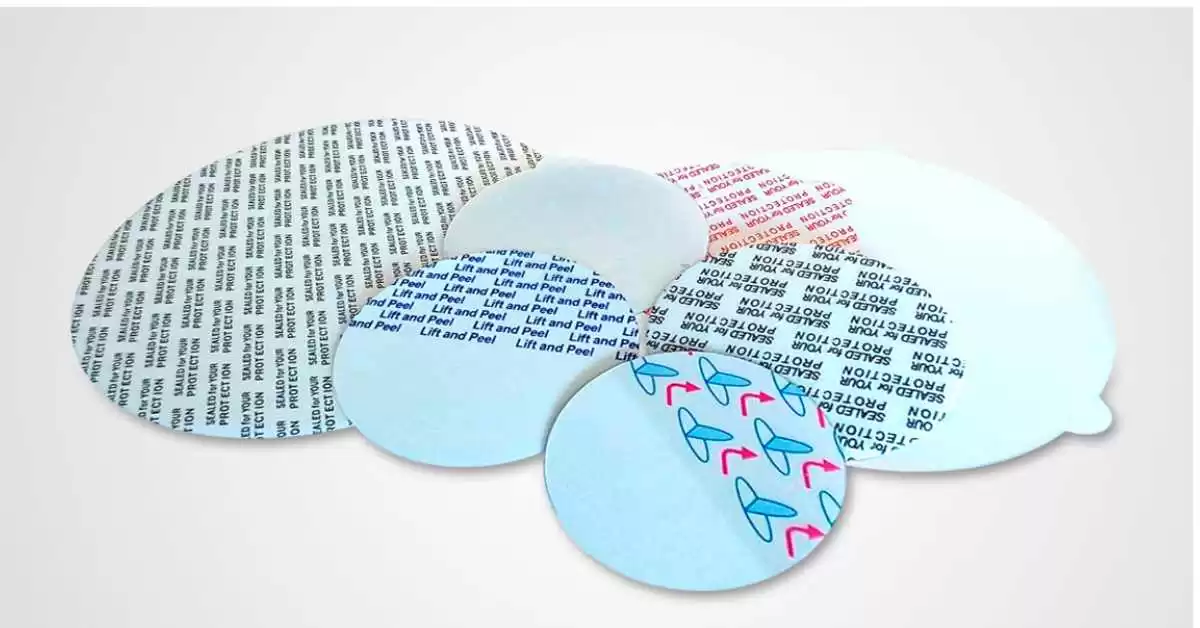
GilPack is happy to announce the launch of a state-of-the-art automatic machine for seamlessly inserting seal liners into caps and cap assembly on our company’s production floor. This innovative addition to our manufacturing process promises to significantly enhance efficiency and productivity. The machine provides close control over the process, with efficient, fast, clean, and quality work – requirements that are especially important in the pharmaceutical and medical industries. The machine meets the medical standard and is suitable for assembling liners inside caps and child-resistant caps.
Incorporating this technology is a natural step in Gil Pack’s development, which began its journey in the production of containers, jars, and bottles intended for the pharmaceutical industry. Over the years, we cultivated cap production capabilities and now, the next step is the automatic assembly and insertion of cap liners. With our new production capabilities, we have achieved significant process optimization, ensuring full documentation of the production steps, which is a crucial requirement in the medical industry. This improvement enhances the quality and provides our customers with increased flexibility in choosing from a wide array of available seal liner options.
Maintaining the safety and longevity of the product
A seal liner plays an important role in maintaining the hermeticity of the packaging and protecting the packed product from the penetration of gases and moisture. Sometimes the liners consist of several layers, providing protection not only during storage and transportation but also after the initial opening of the product. Furthermore, the liner also serves as proof of opening, for the end consumer. Because of the importance of the seal liners function, our new machine is equipped with several sensors that monitor its operation and make sure that the cap that comes out of the machine is in order and without defects that can happen in the process of inserting the seal liners or assembling child-resistant caps.
Types of seal liners available in the market
There is a large variety of seal liners in the market. The choice of the appropriate seal depends on many parameters: the material the bottle is made of, the packaged product and its features, the filling and dispensing line available at the customer’s factory, the way the product is used by the consumer, and more. According to these criteria, we can recommend the structure of the seal, the composition of its layers, its shape, and the way it is connected to the package. Closure liners examples include aluminum liners, paper liners, multilayer liners combining different materials, foamed PE liners, Teflon liners, and more. Each type of liner has its own set of advantages and disadvantages.
Aluminum liners present a significant advantage – an excellent barrier to gases and moisture, extending the packed product’s shelf life. After filling the bottle, the cap is closed, and the aluminum liner undergoes an induction heating process to the mouth of the bottle. The induction process is quick, and clean, and allows for perfect liner adhesion. Thus giving the package both proof of opening and absolute impermeability.
However, there are some disadvantages. For example, the aluminum seal does not allow the final product to pass through a metal detector after filling and closing. Passing through the metal detector is necessary for every manufacturer in the food and pharmaceutical sector and is carried out after filling and closing the cap. In the case of using an aluminum seal, the product passes under the detector before the final packing stage and during this time, between filling and packing, a foreign metallic body may enter the package. We will be happy to share our professional knowledge in this field to overcome this challenge.
Another challenge in using aluminum seals concerns the attachment strength of the seal liner to the bottle. Too strong an attachment may leave liner residue on the container’s mouth, which can potentially contaminate the product. To address this issue, we recommend considering two types of seals: easy-peel seals and lift-n’ peel seals.
Easy peel seals are designed to completely detach from the lid, ensuring a clean and residue-free opening process. On the other hand, lift n’ peel seals come with a convenient tab that allows users to lift the seal without the need to pierce it. This ensures a smooth and effortless opening experience, also minimizing the risk of residue on the container rim.
Both easy peel and lift n’ peel solutions are widely used in various types of seals, not limited to aluminum seals. When selecting the appropriate seal type for your product packaging, it is essential to consider the user’s comfort and convenience. Whether the seal needs to peel off completely or not may depend on specific customer requirements, especially in the pharmaceutical industry, where product integrity is critical. Therefore, incorporating Lift n’ Peel as a feature provides an added advantage to enhance the user experience and meet customer expectations.
Another type of liner is an adhesive paper liner (pressure-sensitive liner) made of a layer of paper with layers of adhesive that are activated under mechanical pressure. After activation, a 24-hour waiting period must happen, until the final adhesive strength is obtained. Attaching the seal liner after bottling at the customer is simple, and does not require induction equipment in the filling line. On the other hand, it exhibits some significant disadvantages: the adhesion mechanism does not always work as required and the sealing strength is sensitive to time and temperature. Storage at a temperature that is too hot causes excess secretion of the adhesive to come out. Therefore, the storage conditions of the packaging and the final product must be observed along the entire value chain. For that reason, the FDA does not recognize pressure-sensitive liners as seals that provide proof of opening, in cases that it is required.
A multi-layer seal liner is another example of a seal that requires induction equipment in the production line. This type of seal liner usually consists of five or six layers where the bottom layer is made of Polypropylene (PP) or Polyethylene terephthalate (PET). The other layers can be of a variety of materials: aluminum, paper, or another polymer.
Differently, a foamed PE seal, Expended PE (EPE), is not attached by adhesion or induction to the bottle. The attachment is obtained due to the elastic properties of the material so that the soft material compensates for imperfections in the finish of the bottle’s spout and provides a hermetic closure to the package. This seal will not provide tamper evidence to the packaging but will improve the hermetic sealing of the cap to the bottle.
Combined seal liners can also be used, such as an aluminum seal in addition to EPE back attached. When combining them, we benefit from the advantages of both worlds: the inherent strength of aluminum, coupled with an additional layer of protection provided by the EPE seal liner, which remains intact even after the initial opening. Similarly, a cardboard-backed seal liner provides some protection after the initial opening. It has an additional role in absorbing moisture from within the package. This seal is often combined with an induction seal that provides hermetic closure and proof of opening.
Packaging products with high chemical reactivity requires the use of a particularly durable seal liner. In these cases, the Teflon seal liner (TPF) has an advantage. Integrating a membrane in the center of the seal can allow ventilation of the contents. This addition is also available for the other types of seal liners and is necessary for products that undergo volume changes during the shelf life of the product. Without ventilation, the package will swell or the sides of the bottle will sink.
Providing the full package
The new sealing machine enables fast, efficient work without manual intervention, which is particularly suitable for the requirements of the medical world. With its help, it is possible to provide a wide solution for caps between diameters of 28 mm and 89 mm. The machine is capable of inserting more than one seal liner into the same lid, according to the customer’s requirement. Personal branding of the liner is also possible with the customer’s logo.
This new technology along with Gil Pack’s other capabilities offers the client a full pharmaceutical packaging solution that includes a container, a cap, and a seal liner. We offer maximum flexibility in product design, size and color, and minimum quantities. Contact us; we will be happy to help you find the optimal lid and seal liner for your product.